With a predetermined cross-sectional shape, the Aluminium extrusion manufacturing process is all about pushing aluminum alloy material into a die. Through the die, a substantial ram forces the aluminum and exits from the die aperture. The entire method is quite straightforward that comprehends on a fundamental level.
This shows with an example- the force implemented can be compared to that used when compressing a toothpaste tube with hands. Just like when you squeeze, the toothpaste comes out in the shape of the tube’s aperture. As an extrusion die, the toothpaste tube’s opening highly performs the same objective.
Types of Shapes That Can be Extruded:
Following are the three main categories of extruded shapes:
- Solid, with no enclosed voids or openings (i.e. a rod, beam, or angle).
- Hollow, with one or more voids (i.e. square or rectangular tube).
- Semi-hollow, with a partially enclosed void (i.e. a “C” channel with a narrow gap)
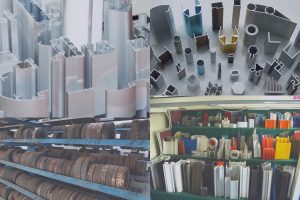
The History Behind Aluminium Extrusion :
Over 100 years ago, this manufacturing process had its earliest beginnings. Joseph Bramah developed the extrusion procedure in 1797 with the motive to produce lead pipes. The method was initially known as squirting and the manual process until Thomas
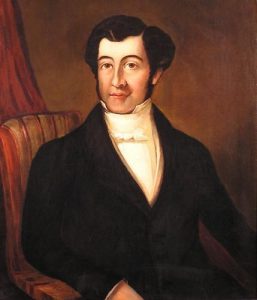
Burr completed the production of the first hydraulic press in 1820. In 1894, Alexander Dick created the hot extrusion method which is currently in modish use. In the Aluminium extrusion manufacturing process, the manufacturers now use non-ferrous alloys and it is all because of the hot extrusion method.
In 1904, there was a rise in aluminum applications in the automobile and construction industries after the first aluminum extrusion press was constructed. At the time of world war, there was a huge increase in the demand for extruding. It was found in use in military applications and the construction of airplanes. The requirement for extruded aluminum started to increase, with top 10 aluminium extrusion companies in India, producing 85% of the country’s requirement. And it is now a part of regular life. You see a car you drive to your every household item, they are all products of this effective manufacturing method.
Why Choose Global Aluminium?
Global Aluminium manufactures premium quality extrusions in different alloys with thicknesses ranging from 0.4mm to 125 mm and profile sizes varying from 4.0 mm to 300 mm subject to the alloys and other specifications. There are more than 15000 dies for 8000 different profiles.
Global Aluminium provides fitting solutions for every conceivable and convincing needs in every field, in different alloys from 1xxx series to 7xxx series and in M, 0, T4, T5, T6, and T8 tempers.