Aluminum is an amazing material. Its one-of-a-kind mix of qualities makes it appropriate for a wide range of applications. When aluminium is exposed to air, it rapidly generates a natural, thin, and transparent oxide film on its surface. This film acts as a barrier against corrosion. When the metal is cut or abraded, the film rapidly re-forms. This glass-hard protective coating is all that is required for surface finishing aluminium in many applications.
However, there may be times when an additional protective or aesthetic treatment on your aluminium extrusion profile is required. Choosing the right finish is an important stage in this process. The incorrect surface finish may appear aesthetically odd or may fail to preserve the metal, resulting in accelerated corrosion and potential structural concerns. Working closely with the top aluminium extrusion profile manufacturer will provide you with the greatest advice on selecting the appropriate surface treatment for your specific needs.
Why Should You Apply a Finish to Your Aluminum Extrusion?
There are three major reasons for adding a finish to your aluminium extrusion:
- To improve corrosion resistance,
- To prime the surface for coating or painting, or
- To improve the beauty of the aluminium.
Environmental Protection: The natural oxide film on aluminium protects it against corrosion, but in harsh conditions, additional protection may be required. Extreme moisture, humidity, and temperature changes, as well as use in near-ocean conditions, can all hasten corrosion. In these cases, an additional finish can assist alleviate the metal’s environmental consequences.
Metal Preparation: An additional finish may be required if the metal surface is to be coated or painted. Anodizing is a chemical process that thickens the natural oxide layer on the surface of metal objects. Anodizing improves the natural corrosion resistance of aluminium as well as its wear resistance.
Finishing may also be required for aesthetic reasons, particularly in consumer products where look is sometimes the first criterion. Different techniques can be used depending on the effect you wish to achieve, such as a brilliantly coloured finished product, a mirror finish, or a textured look.
What Kinds of Finishing Techniques Are There?
It is vital to remember that the surfacing chosen impacts the pricing of the finished product. The higher the production expense, the finer the surface. While there are hundreds of various surface finishes, the majority of them fall into five basic categories:
Mechanical finishes are used to give a surface roughness or to polish it to a chrome sheen. Sanding, polishing, grinding, buffing, and blasting are examples of techniques.
Chemical finishes are applied to profiles by dipping them in a chemical mixture. Etching, which provides a frosted surface look, and bright-dipping, which produces an extremely glossy, specular (mirror) finish, are two of the most common chemical treatments.
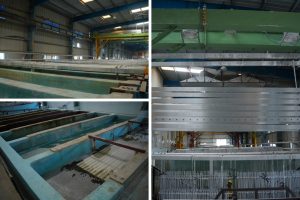
Anodizing is a procedure that involves immersing an aluminium profile in a tank containing an acid-based electrolyte. Aluminum profiles retain their brilliant brilliance while accepting durable and rich colour thanks to the anodizing process.
Liquid coatings come in a variety of paints, including polyesters, acrylics, siliconized polyesters, and fluoropolymers. These applications are available in an almost limitless number of hues, allowing for finishes to suit every preference.
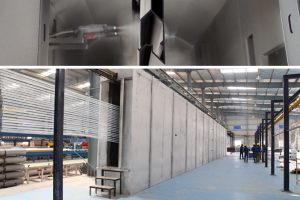
Powder coating creates a decorative surface that is similar to paint but more durable. To create a textured, matte, or glossy covering, dry plastic powder is melted onto the metal. Because no solvents are used, only trace levels of VOCs are discharged into the air, making it essentially pollutant free. Furthermore, unwanted or over sprayed powder can be recovered, reducing waste and allowing it to be disposed of conveniently and safely.