Surface quality and surface appearance of extruded aluminium are of such a type that aluminium finishing is not always necessary for a variety of applications. Because aluminium has such a high corrosion resistance, surface treatments are rarely required for corrosion protection.
There are however a number of other reasons for treating aluminum surfaces, which includes:
- Color
- Electrical Insulation
- Hardness
- A better resistance to wear
- A better resistance to corrosion
- Improving the surface structure
- Reflectivity
Let us look in detail about the two major surface finish treatments used for aluminium extrusion profiles, most specifically at the top aluminium extrusion profile manufacturers:
Anodizing
Anodizing is one of the most frequent surface modifications used for aluminium finishing. It is a procedure used to enhance the thickness of the natural coating already present on aluminium extruded surfaces or to raise the thickness of the translucent film of aluminium oxide.
Visit our Anodizing page for additional information regarding the Anodizing Process for aluminium extrusion profiles.
Anodizing is used in aluminium extrusion to:
- Increase the surface’s corrosion resistance.
- Give aluminium surfaces an electrically insulating covering.
- Create a ‘dirt resistant’ surface so that it fulfils high hygiene criteria (seen in aluminium extrusions used for food processing).
- Creating a surface finish specific to a function (this is seen in abrasion resistant or slip surfaces in machine parts).
- Maintain the “as-new” appearance of a surface.
- Prepare the surface for the application of printing inks or other adhesives by applying a base “coat.”
- Provide a beautiful aluminium finish with long-lasting hues and a high sheen.
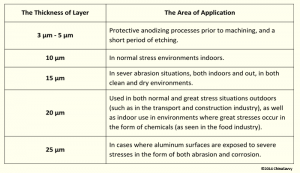
By anodizing aluminium surfaces, manufacturers can gain greater corrosion resistance. This is especially true when the pH range is between 4 and 9. When aluminium surfaces come into touch with powerful alkaline chemicals, they are susceptible to damage. On building sites when extruded aluminium parts come into touch with gypsum, lime, and cement, this is observed. By applying tape to the visible surfaces, this damage can be prevented.
The anodizing process determines the hardness of the oxide layer that forms on the surface of extruded aluminium. Typically, the oxide layer that forms is harder than glass and comparable in hardness to corundum (a crystalline form of aluminium oxide that has traces of chromium, titanium and iron). Oxide layers generated during the anodizing process are transparent and their appearance, whether coloured or natural, depends on the viewing angle. Above 100°C, fine cracks will begin to form in the oxide layer, which is undesired when the coating is applied for decorative purposes. Also notice that bright etched aluminium has a high reflectivity, which is significantly reduced by anodizing processes. In addition, anodized aluminium profiles can be melted and recycled without requiring any pretreatment, but painted aluminium profiles must first undergo a paint stripping procedure.
Powder Coating:
Powder coatings, which are applied to aluminium surfaces and cured without the need of solvents, are available in an almost inexhaustible array of hues. In wet coating facilities, a significant amount of the employed paint evaporates, whereas in powder coating plants, up to 98% of the powder is utilised. The unused powder is then recalculated and reused via a reclamation mechanism.
The Powder Coating Advantages include:
- A material with good formability, indicating that it can be shaped following the coating process.
- The procedure is extremely replicable.
- Powder coated surfaces are suited for outdoor application due to their resistance to UV and corrosion.
- Powder coated surfaces are far more resistant to abrasions and impacts than wet painted surfaces.
- There is no chance of blistering or running with powder coatings.
The coating thickness for this procedure is typically between 60 m and 140 m, and in some instances, the powder coating thickness must be considered when defining the profile’s tolerances and dimensions.
Understand more about Powder Coating of aluminium extrusion profiles in our blog “The complete guide to Aluminium Powder Coating Technology”