Powder coating is a type of coating that is applied to aluminium extruded profile surfaces as a dry powder. It is typically used to protect and improve the appearance of metal surfaces, such as automotive parts, architectural elevations etc. The powder is made up of fine particles of pigment and resin, which are electrostatically charged and sprayed onto the surface to be coated. The charged particles are then heated, causing them to melt and form a smooth, even coating on the surface. Powder coating is a popular choice for many applications because it is durable, long-lasting, and produces a high-quality finish. It is also more environmental friendly than many other coating processes, as it does not produce harmful emissions during the application process.
In general, it is common for powder coating technology to evolve and improve over time, with new developments in pigments, resins, and application methods. Some examples of areas where powder coating technology is likely to continue to advance include the development of new colors and finishes, increased durability and resistance to wear and tear, and the ability to apply powder coatings to a wider range of surfaces and materials.
The Process of Powder Coating:
Powder coating is a type of coating that is applied to a surface as a dry powder. The process of applying powder coating typically involves the
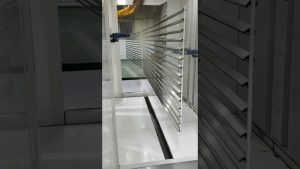
following steps:
- Cleaning: The surface to be coated is thoroughly cleaned to remove any dirt, grease, or other contaminants that may interfere with the coating process.
- Pretreatment: The surface is then treated with a chemical solution to improve the adhesion of the powder coating. This may involve applying an acidic solution to etch the surface, or using a special pretreatment agent to improve the surface’s wettability.
- Application: The powder coating is then applied to the surface using an electrostatic spray gun. The gun applies a negative charge to the powder particles, which are then attracted to the positively charged surface. The particles are then melted and fused together to form a smooth, even coating.
- Curing: After the powder coating has been applied, it is typically heated to a high temperature in order to cure the coating and make it more durable. The temperature and curing time will depend on the specific type of powder coating being used.
- Inspection and Quality Control: After the coating has cured, it is inspected to ensure that it has been applied evenly and to the correct thickness. Any defects or imperfections are corrected at this stage before the coated item is packaged and shipped to the customer.
Components of Powder Coating Technology:
Powder coating technology involves a number of different components, including:
- Pigments: These are the coloring agents that give the powder coating its color and finish. Pigments can be made from a wide range of materials, including organic and inorganic dyes, metallic salts, and other substances.
- Resins: The resins in powder coatings provide the binder that holds the pigment particles together and gives the coating its strength and durability. Different types of resins can be used to produce different properties in the coating, such as flexibility, hardness, or resistance to UV light or chemicals.
- Additives: Powder coatings may also contain a range of other additives, such as flow agents, UV absorbers, and other substances that improve the performance of the coating.
- Electrostatic spray gun: This is the tool that is used to apply the powder coating to the surface. The gun uses an electrostatic charge to attract the powder particles to the surface, where they are then melted and fused together.
- Oven: After the powder coating has been applied, it is typically heated in an oven to cure the coating and make it more durable. The temperature and curing time will depend on the specific type of powder coating being used.
- Inspection and quality control equipment: Powder coatings are typically inspected and tested to ensure that they have been applied correctly and meet the required standards for quality and performance. This may involve using a range of equipment, such as thickness gauges, gloss meters, and colorimeters.
Powder Coating @ Global Aluminium:
We are the largest value added manufacturer of aluminium extrusion profiles. Global Aluminium is one of the best aluminium extrusion companies in India providing single roof solution to all the aluminium extrusion needs including anodizing, powder coating, fabrication and machine works.
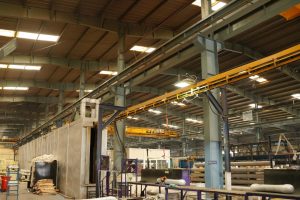
Our powder coating technology includes equipment like Shot Blasting Systems, Robotic blasting systems, Dip and Spray Chemical Pre-treatment plants, Powder Coating Booths and recovery Systems, Dry and Wet type Paint booths/ Spray Booths, Paint Sludge separation and removal Systems, Conveyors, Paint shop -Automation, powder curing Ovens, paint baking/curing ovens, shower tester booths, Teflon coating lines ,enamel coating lines and Effluent Treatment Plants.
Our innovative solutions include renewable energy options for heating and cooling in painting lines and the dry scrubbers with calcium carbonate system replace the conventional water wash booth technology and air exhaust emissions meeting highest standards.
Closed chamber auto conveyorised, auto moving powder spray guns with latest dust collection system for flawless powder coated surface finish (we only use warranty powders)